29 Warehouse Automation Statistics That’ll Blow Your Mind

Warehouse automation.
If you work in the order fulfillment, materials handling, or supply chain industries, then there is a 100-percent chance that you have given at least some thought to the ways that automation has, and continues to, change the nature of your work.
Even if you don’t work in those industries, you’ve undoubtedly heard countless stories about how automation is either going to a.) kill jobs or b.) lead us to a brand-new world of increased productivity.
Are you considering implementing automation in your warehouse, distribution center, or order fulfillment operation? We can help you think through your options.

Whichever version of the future you subscribe to, the truth is that warehouse automation is here to stay, and it’s only going to get more and more sophisticated and advanced as time goes on. Here are 29 statistics that will help you understand the true value that warehouse automation brings to today’s rapidly evolving economy.
The Numbers Behind Why Operations Are Automating
Before diving into statistics specifically focused on how automation can benefit the warehouses and distribution centers that pursue it, it’s important to understand the trends that have led many of today’s order fulfillment operations to pursue automation. Among them are an increased awareness of the technologies, rising labor costs, and rising land/rent/facility costs, all of which encourage business owners to automate to bring costs down.
1. More than 80 percent of the warehouses today have no automation whatsoever. (Source)
However, since last decade ~15 percent of the warehouses are being mechanized, while only 5 percent are using sophisticated automation equipment and solutions. This brings immense market opportunities for the companies in the warehousing automation ecosystem.
2. Worldwide sales of warehouse automation technology (robotics, logistics, etc.) are expected to reach a market value of more than $22.4 billion by the end of 2021. (Source)
Warehouse automation is already big money and is only going to get bigger as more and more companies and operations begin making the switch.
3. As of 2018, an estimated 42% of warehouses and distribution centers expected to move forward with investments in technology and automation. (Source)
The figure, from Peerless Research Group’s (PRG) 2018 annual survey, noted that 40% of survey respondents expected to invest in conveyors and sortation equipment, 25% in robotics, and 14% in AGVs. A further 49% expected to invest in software (such as WES, WMS, or WCS) that runs the equipment.
4. The majority of warehouse and operations managers expect their overall spending on material handling equipment and automation to increase over the next few years. (Source)
52% expected an increase in investment, while 43% expected to spend roughly the same amount annually. Only 5% anticipated a decrease in investments.
5. The average warehouse or distribution center considering investments in automation anticipates spending around $350,000. (Source)
This is an average, which can be skewed by both large and small investments. The median anticipated spending amount, which may be more representative of the responses, was just shy of $70,000.
6. In 2021, the warehouse automation market is expected to grow by more than 38 percent. (Source)
Warehouse automation market in 2019 was estimated at $15 billion up by 10.9 percent from the previous year. In 2020, the total warehouse automation market has experienced decline of 6 percent. However, this year (2021) is estimated to witness growth by almost 38.4 percent to reach $19.5 billion. According to estimates, the market is expected to grow by 1.5x in the mid-term (by 2025) and further expected to cross $37.6 billion by 2030. The calculated compound annual growth between 2021 and 2030 is estimated to be around 10 percent.
7. By the end of 2021, it’s expected that there will be at least 620,000 shipments of various warehouse automation technologies worldwide. By comparison, in 2016, there were about 40,000 units shipped. (Source)
Whether you’re looking at warehouse automation by the amount of money being spent or by the number of units being purchased and put to use, it’s easy to see that the trend is up.
8. Warehouses, distribution centers, and order fulfillment operations employ an estimated 53.7% more workers than they did just 5 years ago. (Source)
In 2016, an estimated 915,000 workers were employed in the sector. As of April 2021, that number hit just over 1,400,000. This increase has been driven by a number of trends, including the continued growth of ecommerce in the United States.
9. Labor costs constitute, on average, 65% of most warehouse facilities’ operating budgets. (Source)
That is a whopping number, surpassing the costs associated with taxes, utilities, rent (or building maintenance), and distribution combined. As the labor market continues to contract, operations are finding themselves needing to pay out higher and higher wages and benefits in order to attract and retain workers.
10. From January of 2020 to September of 2021, the average hourly wage of all warehouse/logistics employees rose by nearly 10%, some of the fastest wage growth since data began being collected. (Source)
A tightening job market has led to a significant increase in worker compensation, beating inflation over the same period. Since payroll is one of the single largest expenses for most operations, this has impacted the bottom lines of many, encouraging a switch to automation for cost savings. This trend has only continued in recent years, and has become especially salient in light of the coronavirus pandemic which has forced many businesses to fight for workers by offering higher wages.
11. A typical warehouse with 100 non-supervisory employees cost more than $3.7 million in labor expenses annually as of March 2018. (Source)
The average non-supervisory warehouse employee worked 40.9 hours weekly and made $17.61 per hour. This math doesn’t include the cost of health insurance, short- and long-term disability insurance, vacation, overtime, and other costs associated with employing workers.
12. In 2020, there were approximately 5 workplace injuries for every 100 full-time workers in the warehouse/storage industry. (Source)
Further, it’s estimated that 5% of all warehouse workers will experience some sort of injury on the job each year.
Warehousing and storage involve a lot of moving pieces, often with the use of heavy machinery. Humans, being humans, sometimes make mistakes due to distraction, exhaustion, negligence, etc. Automation is seen by many operations as a means of reducing this rate of injury by removing the human element from the most dangerous of processes.
13. The warehouse and transportation industry sees costs in excess of $84 billion per week due to serious, non-fatal injuries. (Source)
That is a staggering sum, which could be put to better use investing in growing the business and the industry, or else returning to shareholders and investors. Taking steps to reduce the human element, which is prone to accident and error, by automating the most monotonous and repetitive tasks, is an excellent means of reducing the number of workplace accidents.
14. The average size of a warehouse today is more than 180,000 square feet, compared to 127,000 square feet. (Source)
Today’s warehouses take up over one-third more space than they did a decade ago and are nearly three times more voluminous than they were prior to the year 2000. Stemming from an increase in SKUs and other factors, these larger footprints have led to increased facility costs. Warehouses looking to squeeze more usable space out of smaller footprints are increasingly looking to automation to get more out of the space they already have.
15. Due to increased footprints, average warehouse renting rates have increased by a massive 28% in recent years. (Source)
This increase, again, speaks to a desire to get more out of existing spaces.
16. Only 9% of distribution centers and warehouses handle only full pallet orders, compared to 46% that handle a mixture of pallets, cases, split cases, and pieces. (Source)
In the past, many DCs could operate by shipping only full pallet orders. The rise of e-commerce has brought with it a rise in split case orders and even single-unit shipments, which rely much more heavily on automation technologies to be efficient compared to full-pallet orders.
17. The average warehouse or order fulfillment operation has see an 18.5% increase in the number of SKUs handled. (Source)
SKU proliferation—an increase in the number and variety of products handled by an operation—can lead to a multitude of issues surrounding inventory visibility and accuracy, especially when orders are picked and inventory is logged manually. As inventory continues to grow and become more complicated, it is expected that more and more operations will convert to fully-integrated inventory management systems.
18. According to a survey of warehouse and DC operations, the largest challenges they’re facing include insufficient space (43%), inability to attract qualified employees (39%), outdated storage, picking, and handling equipment (34%), and inadequate information systems support (32%). (Source)
Whether the problem is space, workforce, or systems related, most can be remedied or at least addressed by leveraging today’s advanced technologies. A skilled systems integrator will be able to help you understand your options, and guide you toward the solution that will best empower you to reach your goals despite the constraints of your facility.
How Warehouse Automation Technologies Can Improve Efficiency
Beyond simply bringing down costs, automation technologies have incredible potential to help operations become more efficient, more accurate, and more productive. Below are some statistics illustrating how different technologies can improve the performance of an order fulfillment operation.
19. On average, retail inventory is accurate only 63% of the time. (Source)
Because having an accurate picture of your inventory is crucial to successfully running and growing any operation, improving inventory visibility is one of the most pressing concerns in warehouses, DCs, and retail today. More advanced picking technologies such as RFID scanners, pick-to-light, and inventory management systems can make understanding your inventory much more manageable.
20. When operations upgrade their pick/inventory systems from paper-and-pencil to a more integrated form of order processing, they enjoy on average a 25% gain in overall productivity, a 10-20% gain in space use, and 15-30% more efficient use of stock. (Source)
By using a Warehouse Management System (WMS) to integrate their orders, pick systems, and inventory management, warehouses stand to dramatically improve their performance.
21. Pick-to-Light systems can improve pick rate productivity by 30-50%. (Source)
Thanks to increased accuracy, shorter order cycle times, increased throughput, and other factors, pick-to-light systems have a lot of potential to improve an operation’s bottom line.
22. Pick-to-Light, RFID, and Pick-to-Voice technologies reduce picking error rates by 67% compared to manual paper-and-pen methods. (Source)
Again, by removing the human element from the equation, order fulfillment operations can enjoy increased accuracy, decreased error, and more general productivity.
23. Walking and manually picking orders can account for more than 50% of the time associated with picking. (Source)
The simple fact is that moving from location to location within a warehouse takes time, especially when done manually. By leveraging automation technologies like sorters, AS/RS, conveyors, and more, time spent “walking” can be reduced by up to 40%.
24. The average order picker can pick between 60 to 80 picks per hour, compared to a pick rate of up to 300 picks per hour when leveraging sorters and conveyors. (Source)
By reducing travel time, conveyors and sorters can dramatically increase the overall productivity of an order fulfillment operation.
25. Robotics and automation technologies have increased labor productivity by about 0.35% annually, which may not sound like much, but is on par with the impact felt by the steam engine from 1850 to 1910. (Source)
As robotics and other automation technologies are applied to more and more industries and tasks, their impact is being felt more and more. There is potential that in the next few years, the impact of these new technologies will even outpace the impact experienced in the industrial revolution.
26. Automated Storage and Retrieval Systems (AS/RS) have the potential to increase order accuracy levels to above 99.99%. (Source)
Order accuracy has always been important and has only gotten more important as customers have grown accustomed to increased service levels. By integrating directly into a warehouse management system, AS/RS removes a large percentage of human error associated with picking and shipping orders.
Effect of The 2020-2022 Supply Chain Crunch On the Warehouse Industry
The emergence of the coronavirus pandemic in the spring of 2020 put unprecedented stress and pressure on the global supply chain, as it caused economies around the world to grind to a halt. People were encouraged to stay home. Stores and businesses had reduced hours, or were closed completely. The warehouse and logistics industry was one of the few industries to never shutter—and in fact played an essential role in keeping society from collapse.
While the full effect of the supply chain crunch on the warehouse and logistics industry is unknown at this time, below are a few interesting statistics about the ways in which it has already impacted the industry and its move toward automation.
27. In Q1 of 2020, before the pandemic emerged, ecommerce sales in the United States were an estimated $160 billion. In Q2, during the heart of the pandemic, that total jumped to $211 billion. (Source)
Due to the nationwide shutdown and limited availability of many products in brick and mortar retailers, more and more buyers found themselves turning to ecommerce for their shopping. While ecommerce has been growing for years, this essentially pulled forward much of that growth in one massive surge of demand.
Companies that were prepared for this demand were able to flourish, delighting customers and turning them into repeat buyers. Meanwhile, those who were unprepared for that demand were forced to play catch up, and may have lost customers due to unreliability.
Technologies such as autonomous mobile robots (AMRs), which are relatively easy to scale up or down in order to meet changes in demand, proved to be an essential tool for operations during this time.
28. The International Finance Corporation, a part of the World Bank Group, expects that we are in the middle of a fundamental restructuring of the global supply chain. (Source)
The challenges of the past two years have highlighted the fragility of having such a global supply chain, where weakness or disruption in one part of the world can have massive impacts elsewhere. Even today, global logistics has yet to fully recover, and many in the United States are facing long shipping times for products that they order (if they are able to find them at all).
With this in mind, many businesses and governments are taking steps to expand their local supply chain to better accommodate these challenges. Operations that make smart investments now are expected to reap the reward in the coming years.
29. Controlling the pandemic within facilities has required a rethinking of workflows and processes. (Source)
In order to spread, COVID-19 requires an individual to be within close enough proximity to others. Without this proximity, the disease cannot jump to a new host. With this in mind, preventing outbreaks within warehouses and facilities has required businesses to prioritize social distancing, and to find ways of compartmentalizing workers away from each other.
This has caused many operations to rethink their internal workflows. Some have achieved this by staggering their shifts or by increasing the time between picking waves. Others have invested in individual workstations where workers interact with fewer (if any) coworkers. Still others have invested in “co-bots” which serve to make an individual worker more productive, as a partner might.
Which option makes the most sense for you will depend on your operation, your workflows, and your challenges. But the fact remains that intelligently rethinking how your workers work can help you prevent illness in your facility (whether COVID-related or not) and increase your efficiency.
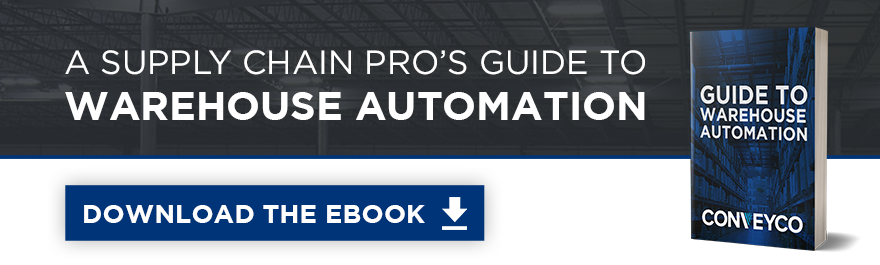