12 Warehouse Safety Statistics to Guide Your Design Build

Worker safety should be a critical consideration for every business owner, regardless of the industry they operate in. It is especially critical in an industry like order fulfillment and warehouse management, which requires personnel to interact with heavy machinery and complex equipment on a daily basis.
That is why it is so crucial for warehouse and supply chain managers overseeing a warehouse design, renovation, or optimization to keep safety considerations in mind every step of the way. After all, safe facilities enable employees to work more efficiently and allow an employer to limit accidents, preventing expensive damage to equipment, inventory, and workplace morale.
Download Our Top Order Fulfillment Key Performance Indicators Ebook
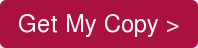
Below we’ve gathered some of the most poignant warehouse safety statistics available. We encourage you to reference them before embarking on your warehouse or distribution center design project, and to leverage them in order to improve worker compliance with any safety standards that you have in place.
1. It is estimated that 5 percent of all warehouse workers will experience an injury on the job each year. (Source)
The cost of these injuries to an employer can be substantial. In the event that the incident was caused by negligence on the part of the facility manager, costs could range from tens of thousands to hundreds of thousands of dollars, especially if litigation is involved. Even for incidents in which the employee is at fault, the employer is likely to face expenses: In the form of lost productivity, increased insurance costs, the hiring of temp workers, etc.
2. The transportation and shipping industry is behind only service members (firefighters and police) in terms of how many accidents it experiences as an industry. (Source)
This is largely due to the complex nature of the work involved. Though some blame an increased use of technologies for these injuries, most are caused by human error and not technological malfeasance. In fact, many automated warehouse technologies improve workplace safety by removing the possibility of human error from the equation.
3. According to the National Safety Council, preventable workplace deaths have increased nearly 18% since 2009. (Source)
Workplace deaths have not only increased since 2009, but they are also outpacing the number of hours worked by about 6%. The concerning increases are gaining attention from political and business leaders as well. Last spring, Mark Vergnano, the chairman of the NSC Board of Directors, made a request to recommit to protecting works from death and injury while remembering those who lost their lives on the job by acknowledging Workers’ Memorial Day on April 28th.
4. Warehousing and Storage makes up 25% of the largest employers of material moving machine operators—by far the highest among any industry. (Source)
This metric should come as no surprise, as warehouses require full time supervision and work to ensure shipping demands are being met. Overall, the Bureau of Labor Statistics reports that material machine operators held about 741,500 jobs in total last year. Safety concerns, particularly working fatigue and overexertion are concerns for warehouse managers, especially when considering overtime and overnight shifts worked by machine operators.
5. Serious, non-fatal injuries cost $84.04 million a week in the transportation and warehousing industry (Source)
This data spearheaded by Liberty Mutual includes metrics from the U.S. Bureau of Labor Statistics and the National Academy of Social Insurance. Collectively, this information highlights what non-fatal injuries caused employees to miss more than five days of work. Those events were then ranked by total workers compensation costs. The report also found nearly 30% (27.6%) of the percentage cost for non-fatal workers compensation claims involved overexertion involving outside levels. Falls on the same level accounted for 17% of the total costs for non-fatal claims.
6. In 2017, costs in occupational safety for all industries totaled $161.5 billion and of the list of preventable fatal injuries, warehousing and transportation ranked number 2 overall (behind construction). (Source)
These metrics provide the financial strains on organizations when dealing with injuries to workers. To further break these numbers down, wage and productivity losses totaled over $50 billion, medical expenses totaled over $34 billion, and administrative expenses for work injuries totaled $52 billion. Additionally, the cost per worker was $1,100, which includes the value of goods each worker must produce to offset the cost of work injuries.
7. There were 2.8 million nonfatal workplace injuries and illnesses reported by private industry employers in 2017. (Source)
This annual report released in November takes a look at employer-reported workplace injuries and illnesses. The rate of cases in 2017 totaled to 2.8 per 100 full-time equivalent (FTE) workers. Additionally, private industry employers reported nearly 45,800 fewer nonfatal injury and illness cases in 2017 compared to the previous year. The Survey of Occupational Injuries and Illnesses also accounts for this data as well.
8. The number of “days away from work” cases in warehousing and storage rose by nearly 3,000 cases to 17,390 total cases in 2017. (Source)
The Bureau of Labor Statistics estimates that nearly one-third of nonfatal occupational injuries and illnesses resulting in days away from work. Overall, there were over 800,000 cases of occupational injuries and illnesses that resulted in days away from work in the private industry. Interestingly enough, this statistic remained essentially unchanged from the previous year.
9. That same report revealed that incidents resulting in overexertion and bodily reaction rose to 8,310, which is an increase of 1,350 cases from the previous year. (Source)
Proper lifting is crucial to avoiding overexertion and injury in the warehouse. Proper lifting is not just limited to human limitations either. Knowing when and how to use equipment is a critical factor in avoiding injury. With shipping demands increasing seemingly everyday, warehouses are pressed into loading more packages in a shorter amount of time. The stresses of higher demands can cause worker fatigue, so warehouse managers must ensure all workers are following proper safety protocols and techniques.
10. The American Supply Association reports that 25% of all industrial accidents occur at the loading dock, many of which are associated with the use of forklift trucks. (Source)
Additionally, this report shows for each accident that does occur, there are about 600 near misses. It’s imperative that warehouse managers properly train workers on using the loading dock properly. Worker fatigue and carelessness can be deadly around the loading dock, so it’s critical that proper safety regulations are being followed. Order fulfillment is the ultimate goal of each warehouse, but never at the expense of worker safety.
11. OSHA reports 36% of the nearly 100,000 forklift accidents at the workplace in 2015 caused either serious injury or death. (Source)
Forklifts may not be the fastest machines, but don’t let their speed fool you. With an average forklift weighing around 9,000 pounds, the risk of injury is incredibly high. With a heavier weight in the rear to counter the front weight on the forks, forklifts are difficult to stop. Not to mention, most forklifts only have stopping power on their front wheels.
12. Nearly 100 employees are killed and 95,000 are injured every year while operating forklifts in all industries. (Source)
Beyond just the shipping and warehousing industry, there are safety risks in operating a forklift across all industries. As previously above, forklifts are heavy and hard to stop. To help prevent injuries, OSHA recommends training operators on a yearly basis and maintaining forklifts in prime condition at all times. Also, it’s important to ensure all operators are experienced and alert when driving forklifts.
The Bottom Line
Ultimately, a successful warehouse design will be one that enables an order fulfillment operation to process its orders quickly, accurately—and safely. Prioritizing safety not only reduces accidents, but also creates a more productive environment.
Equipment choice, especially, can make a tremendous difference in workplace safety, as is illustrated by the statistics about manual forklifts above. Making the switch to automated options—like autonomous mobile robots—for the transportation of inventory can, for example, help your facility instantly become safer simply by removing human error from the equation. A trusted systems integrator can help you identify these and other opportunities to maximize the safety and efficiency of your operation.