Benefits of Automatic & Semi-Automatic Palletization & Wrapping

For warehouses and distribution centers catering to retail order fulfillment, there are a slew of options to help make your operation more efficient, productive, and profitable.
Autonomous mobile robots can help streamline your inventory receiving and replenishment; automated storage and retrieval systems (AS/RS) and goods-to-person can improve your picking processes; automated sortation can help you process orders more effectively. Virtually every step of the order fulfillment process can be either automated or otherwise augmented and streamlined by technology.
One area that doesn’t always get the attention it deserves, however, is the final step in the process before many orders go out the warehouse doors: Palletization. Not enough organizations strategize on palletization until it’s already become a problem. That’s a shame, because even this step can be improved upon in order to increase throughput and operational efficiency.
Download Our Guide to Warehouse Automation
Below, we discuss the benefits of automated palletization and three potential options you can leverage in your operation, from mostly manual to semi-automated to fully-automated solutions.
3 Ways to Automate Your Palletization Processes
The Stack & Wrap mixed layer palletizing packstation is a form of automated palletizing which can be leveraged in either a semi-automated, increasingly automated, or fully automated manner.
It works like this: The pallet itself sits within a mechanism that is lowered down to ground level as the pallet is built. This means that the top layer of the pallet is always at waist-height—an ideal, ergonomic position for workers, who manually build each layer of the pallet.
The workstation is fed cases via a belt conveyor. On the top level, one or two operators standing on either side of the pallet receive the product and move it into position on the pallet. Once the layer is complete, the pallet is automatically lowered so that the next layer of product can be created on top of the completed layer. As the pallet is lowered, it is automatically stretch wrapped in order to both prepare it for final transportation and also to offer structure and stability for the layers yet to be built.
Need expert advice? Book a free consultation with one of our solutions consultants today!

When the pallet is complete, it is discharged onto a pallet conveyor, and a new pallet is automatically moved into position so that the operators can repeat the process. At the end of the pallet conveyor, a forklift operator receives the pallet and brings it to storage or shipping.
As mentioned above, this technology can be leveraged in one of three ways:
1. Semi-Automated
This is the situation described above. While the pallet is automatically wrapped as it is lowered, the process of actually building the pallet is done by one or two human operators. Even so, substantial benefits are realized, including increased efficiency and extremely fast throughput rates compared to a fully manual process. This is achieved due to the fact that the system always keeps the pallet’s top layer at an ergonomic height, which enables the worker to perform more efficiently.
Additionally, by automatically wrapping the pallet as it is built, the system adds strength and stability to the pallet. This makes it possible to build taller pallets without the risk of collapse that might otherwise occur.
The configuration of the system is also especially helpful in saving space. Because the system is two levels, approximately half the space is required to palletize and wrap compared to conventional palletization.
2. Increasingly-Automated
This same process can be further automated by pairing the system with an AMR-based transportation system, which would receive the finished pallet in lieu of a manual forklift operator. The AMR would then transport the pallet wherever it needs to go in the facility, reducing the need for a forklift fleet and reducing labor costs even further.
3. Fully-Automated
Finally, the process may be fully automated by building upon scenario two mentioned above. The main difference is that instead of human operators building the pallets, you can leverage one or multiple robotic arms, which would receive the cases from the product conveyor and then build the pallet layers without any human touches whatsoever. This scenario essentially eliminates the need for any labor associated with palletizing in your operation.
The video below demonstrates how robotic arms can be leveraged in palletization:
Benefits of Automated & Semi-Automated Palletizing
Leveraging a palletizing system such as the one described above can help your operation realize a number of benefits, regardless of whether you choose to pursue semi- or full automation. These include:
- Save up to 50% of otherwise wasted floor space
- Improved ergonomics and fewer injuries
- Increased efficiency and throughput
- Reduced labor costs
- More efficient use of floor space
- The ability to build taller pallets
Leveraging Automated Palletizing in Your Operation
If you are interested in potentially automating your palletizing processes, it’s important to understand the options available to you and to think critically about which is the best scenario for your business. Do you hope to become semi-automated, or does full automation appeal to you?
A trusted systems integrator can help you weigh your options and ensure that your palletizing systems are fully integrated with the rest of your operation. Schedule a consultation now to speak with a member of the Conveyco team!
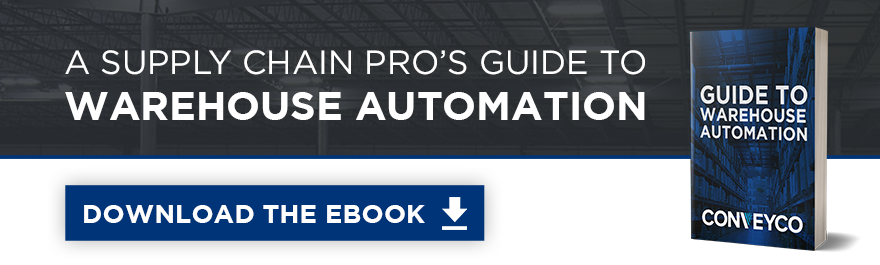