5 Ways to Prepare Your Warehouse for Peak Holiday Season

It may be strange to think about the holidays in the high heat of August, but as anyone working in order fulfillment or retail knows, the holiday season is right around the corner. Depending on the specifics of which industry your business serves, it could be as little as 30 days away; if you’re lucky, you might have upwards of 90 days before the real rush begins.
Whether you’ve got 30 days or 90 days, the truth is that there really isn’t much time to prepare your operation for the challenges that come with peak season.
Need an Expert Opinion?

If you plan to ramp up hiring of temp/seasonal workers to accommodate the rush, how will you address the growing labor shortage impacting the industry? If you’re concerned about your ability to have enough inventory on hand for holiday orders, have you found ways to optimize and reclaim your floor space? If you struggle with order accuracy during periods of typical demand, do you have a plan in place to address this issue when it is compounded by higher throughputs?
While we’re at it, do you have an estimate as to how much your business is expected to jump during peak season? More importantly, do you have a plan in place to address capacity, inventory, throughput and labor to make sure that you hit these numbers?
If reading these questions has caused you to start sweating, we apologize. But these are serious concerns for warehouses and operations of all sizes. If you’re going to get ahead of them, you need to start putting your time and energy toward them now.
Not sure what steps are still realistically in reach before the crunch of the holiday season hits in full force? Below are some recommended steps that you can and should take now in order to prepare, as well as some ideas that you can use to start preparing for next year—now.
Short-Term Tips to Prepare for Peak/Holiday Season
1. Embrace maintenance.
While unexpected downtime on an essential piece of equipment is never a good thing, it is arguable much worse during peak season, when your people and equipment must be able to cope with higher throughputs and demand. That’s why it is so critical that you take the time now to ensure that your equipment will be able to perform under the increased stress that comes with the holidays.
Use the lead-up to peak season to:
- Schedule and complete preventative maintenance for your most critical systems (Think: Sorters, conveyors, AS/RS, etc.)
- Stock up on spare parts that have the greatest potential to break down or impact your systems
- Ensure that your maintenance agreements for both hardware and software are active and up to date
2. Think about your slotting practices.
Slotting is simply the process of organizing the inventory within your warehouse. An effective slotting process will result in inventory being stored in the optimal location within your facility, which can have the effect of reducing travel time, reducing the number of touches an item received, improving order accuracy, and simply making your picking processes more efficient.
If you are concerned about your operation’s ability to meet the demands that it will experience during peak season, take the time now to evaluate your slotting practices, and consider what changes you can make in the short term to help your people work more efficiently. Grouping inventory by product affinity, for example, is one strategy that can have serious positive impacts on your operation.
Not sure that you can evaluate your slotting practices and put new processes in place before the holiday rush begins? A systems integrator may be able to help.
3. Plan for labor issues.
If you are going to be relying on temp or seasonal workers in order to cover the increased demand of the holidays, it’s better to start locking down bodies now—before the season is in full force. Waiting even just a few weeks can cause your available labor pool to shrink substantially, driving up your hiring costs and making it even more difficult to fill open positions.
Additionally, think about how you will train these workers once they are hired. Ideally, you should have everyone up to speed on your processes before the rush of the holiday season begins.
4. Tie up the loose ends.
If you are in the middle of undertaking a major new initiative or implementing a change to your processes or technology, do your best to finalize and resolve them before the stress and confusion of peak season hits.
Also be sure to update any SOPs to reflect these changes so that your regular employees and seasonal/temp workers have a clear understanding of how to do their jobs. Training your workers on new procedures and technologies is hard enough during the typical months, never mind when your throughput is tripled, quadrupled, or more. You need your people and equipment at its absolute best if you’re going to make it through peak season.
5. Remember to collect data.
If you plan to make serious changes to your operation for next year’s holiday season, you need to begin preparing for those changes today. The best thing that you can do right now is to make sure that you have a system in place that will allow you to collect data about how your operation performs during the impending holiday season—data which will be invaluable in informing the optimizations and changes that you hope to make in the future.
How is your operation performing across key metrics during the holiday season? What are your throughputs? How do they compare against your typical, off-peak day? What is the average order cycle time during peak? What about accuracy? Etc.
If you plan to make serious changes to your operation for next year’s holiday season, you need to begin preparing for those changes today. The best thing you can do right now will be to collect data. What are your throughputs? How is your operation performing across key metrics during peak season? Etc. This data will be invaluable in informing any changes you make.
It’s Not Just About the Short-Term
Once the season is over, it’s fine to take a day or two to celebrate—you’ve earned it. But then it’s time to begin planning for next year, especially if you’ve got major challenges to overcome or if you have larger initiatives that you are working toward.
Your greatest opportunities for improvement over the long-term are to:
- Identify and improve bottlenecks within your facility so that your people and equipment can be more effective
- Implement automation that can scale with your business, such as AMRs, AS/RS, pack-out systems, etc.
Ready to get started? Schedule a free consultation with one of our expert systems integrators to see how you can prepare for this and future holiday seasons.
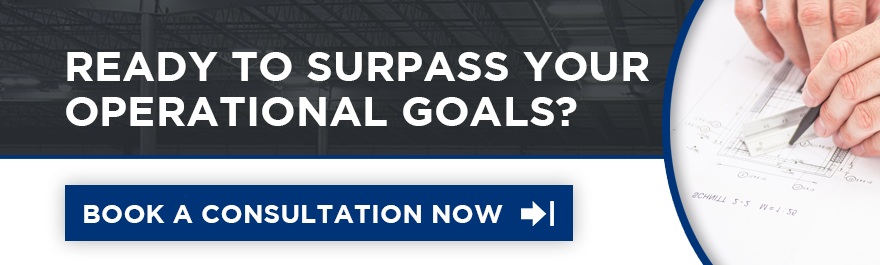